Are you designing a product that requires a permanent magnet but unsure which one to choose? Selecting the right permanent magnet is crucial for the functionality and efficiency of our design. So, to ensure the success of your design, keep reading to learn more about how to choose the perfect permanent magnet.
Key questions when choosing a permanent magnet?
There are all great factors to consider when choosing a permanent magnet for our design. Here is a summary of each point:
- The required magnetic strength?
- The object that the magnet will hold, lift, or attract?
- The temperatures that the magnet will be subjected to?
- Whether the magnet will be exposed to corrosive conditions or substances?
- Whether the magnet will be exposed to demagnetizing or destabilizing factors?
- What is the equipment expected lifespan where the magnet will be used in?
- Any size or weight constraints for the magnet?
- What is the material and volume of the object that the magnet will be attached to?
- What are the project’s budget and the magnet’s unit price?
To determine the answers to the above questions, it is necessary to have a deeper understanding of the various factors that influence the selection of a permanent magnet, such as the magnetic strength required, the operating environment, and the cost.
It can be overwhelming, but it is essential to ensure that you select the most suitable option for your specific needs. We will guide you through determining the correct type of magnet for your project.
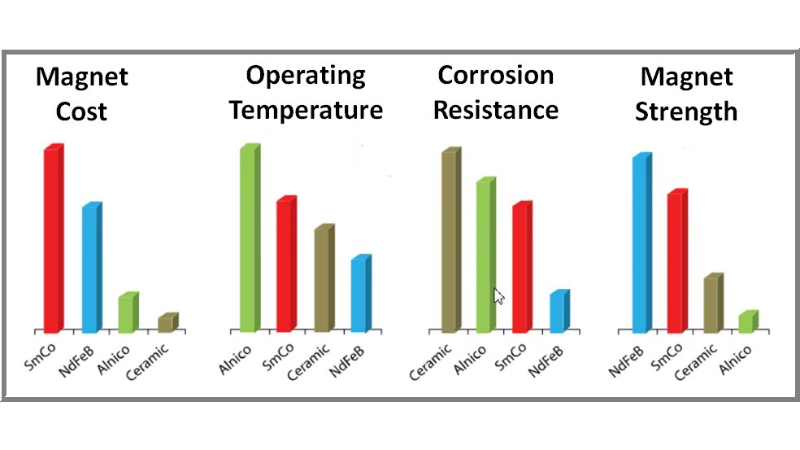
Understanding the Types of Permanent Magnets
Four main types of permanent magnets are available, including Neodymium, Samarium Cobalt, Alnico, and Ferrite magnets. Each type has unique properties that should be considered when selecting a magnet for your application. To choose the best magnet for your needs, it is vital to understand the differences in these properties and how they may affect the magnet’s performance in your design. Let’s explore each of these options and their unique characteristics:
Table(1): Main Types of Permanent Magnet
Permanent Magnet | Element Symbol | Components | Brief Usage |
Neodymium/Neo | NdFeB: Nd (neodymium), Fe (iron), B (boron) | An alloy of neodymium, iron, and boron. | They are the strongest type of permanent magnet and are often used in applications where a very strong magnetic field is required. |
Samarium cobalt | SmCo: Sm (samarium), Co (cobalt) | An alloy of samarium and cobalt. | They have higher temperature stability than neodymium magnets, making them a good choice for high-temperature applications. |
Alnico | AlNiCo: Al (aluminum), Ni (nickel), Co (cobalt), and other elements | An alloy of aluminum, nickel, cobalt, and other elements. | They have lower magnetic strength than neodymium and samarium cobalt magnets but higher temperature stability and corrosion resistance. |
Ferrite/Ceramic | Fe2O3 (iron oxide) and ceramic materials | A mixture of iron oxide and ceramic materials. | They are a lower-cost alternative to neodymium magnets and are commonly used in motors and speakers. |
1. Considering the Magnetic Strength
The magnetic strength of a magnet is related to its maximum energy product (BHmax), and the higher the BHmax value, the more energy the magnet can store and the stronger it is.
Neodymium Iron Boron (NdFeB), Samarium Cobalt (SmCo), Alnico, and Ferrite are all types of permanent magnet material that are offered in different grades, and each grade can have a different maximum energy product (BHmax). The below chart is the typical comparison:
Table (2): Some Magnetic Properties of Main Magnet Grades
Permanent Magnet | Max. Energy Product BH (max) | Coercive Force Hc (min) | Intrinsic Coercive Force (Hci) | Typical Residual Induction Br (max) |
Types/Units | MGOe | Oersteds | Oersteds | Gauss |
Neodymium 35 | 33-36 | ≥10900 | ≥12000 | 11800 |
Neodymium 40 | 38-41 | ≥11400 | ≥12000 | 12700 |
Neodymium 42 | 40-43 | ≥11500 | ≥12000 | 13000 |
Neodymium 45 | 43-46 | ≥11600 | ≥12000 | 13300 |
Neodymium 48 | 46-49 | ≥11600 | ≥12000 | 13600 |
Neodymium 52 | 50-53 | ≥10000 | ≥11000 | 14100 |
SmCo 18 | 16-18 | ≥8100 | ≥16000 | 8700 |
SmCo 20 | 19-21 | ≥8500 | ≥16000 | 9200 |
SmCo 22 | 20-22 | ≥8900 | ≥16000 | 9500 |
SmCo 24 | 22-24 | ≥9100 | ≥18000 | 9900 |
SmCo 26 | 24-26 | ≥9400 | ≥18000 | 10400 |
SmCo 28 | 26-28 | ≥9500 | ≥18000 | 10700 |
SmCo 30 | 28-30 | ≥9900 | ≥18000 | 11000 |
Alnico 5 (cast) | 5.5 | ≥650 | ≥640 | 12500 |
Alnico 8 (cast) | 5.3 | ≥1450 | ≥1860 | 8200 |
Alnico 5 (sintered) | 4.2 | ≥600 | ≥630 | 1200 |
Alnico 8 (sintered) | 4.0 | ≥1500 | ≥1690 | 8200 |
Ceramic 1 | 1.05 | ≥1860 | ≥3250 | 2300 |
Ceramic 5 | 3.4 | ≥2500 | ≥2800 | 3800 |
Ceramic 8 | 3.5 | ≥3200 | ≥3400 | 3900 |
BHmax (Maximum Energy Product)
BHmax, the maximum energy product, is expressed in kilojoule units per cubic meter (kJ/m3) or mega-gauss-oersted (MGOe).
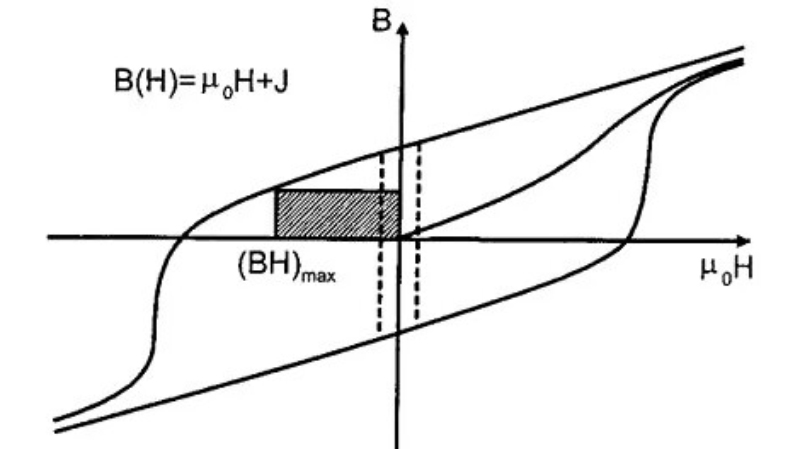
From Table (2), the range of BHmax values is extensive for different types of magnets, with flexible ferrite magnets having a low value of fewer than 1 MGOe and neodymium-iron-boron (NdFeB) magnets having the highest value of 53 MGOe.
It is important to consider the impact of BHmax on volume when designing a magnetic circuit. Higher BHmax magnets require a smaller volume of magnetic material to generate a given flux, while lower BHmax magnets require a larger volume. For example, it would take 53 times more volume of ferrite magnet to generate the same 1 MGOe flux as a NdFeB magnet.
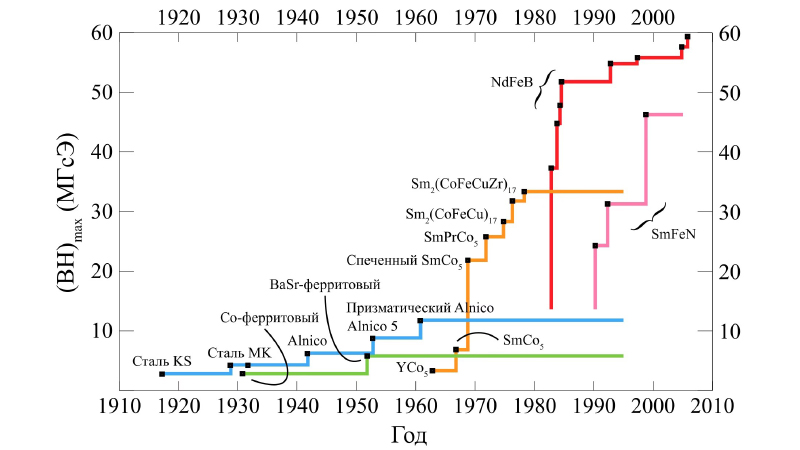
In applications where weight, length, size, or geometry are limited, it is generally more efficient to use high BHmax magnets and the smallest possible volume of magnetic material. In applications that are not weight sensitive, it may be more practical to use a larger volume of low BHmax magnet material to achieve the desired flux density.
Intrinsic coercive force (Hci):
In addition to BHmax, the Intrinsic Coercive Force (Hci) and Residual Induction (Br) of a magnet can also be related to the magnet’s magnetic strength.
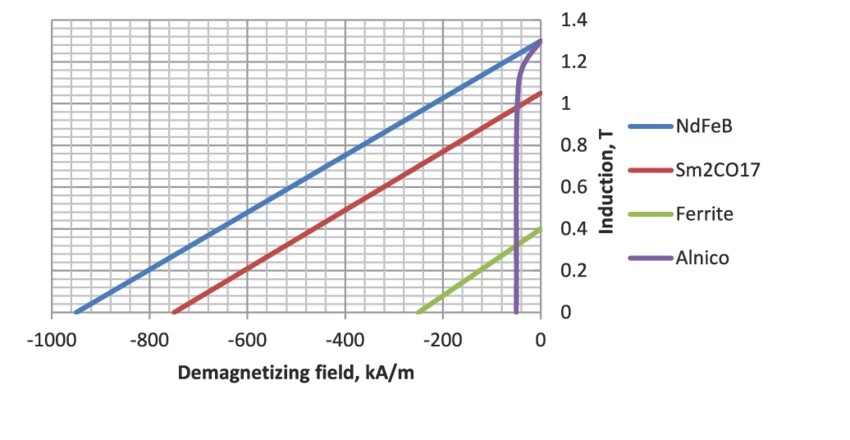
The Hci of a magnet is a measure of its resistance to being demagnetized, and a magnet with a higher Hci value is more resistant to demagnetization and is less likely to lose its magnetism when subjected to external magnetic fields. From Table (2), we can see different magnet materials can have different Hci values:
NdFeB magnets have a very high Hci value, making them highly resistant to demagnetization.
SmCo magnets also have a high Hci value and are resistant to demagnetization. They are known for their stability at high temperatures and are often used in high-temperature applications.
Alnico magnets have a moderate Hci value and are less resistant to demagnetization than NdFeB or SmCo magnets.
Ferrite magnets have a low Hci value and are relatively easy to demagnetize.
Residual induction (Br):
The Residual Induction (Br) of a magnet is a measure of the residual induction of the magnet, which is the magnetic field strength remaining in the magnet after an external magnetic field is removed. It is typically expressed in units of gauss (G). Magnets with higher Br values will have a stronger residual induction and will likely perform better in applications that require a strong residual magnetic field.
The difference among magnets’ remanence (Br) can be seen by comparing each type of magnet’s numerical values of the Br.
For example, the Br value of a high-grade NdFeB magnet may be around 14,000 G, while the Br value of a lower-grade NdFeB magnet may be around 12,000 G. Similarly, a high-grade SmCo magnet may have a Br value of around 10,000 G, and an Alnico magnet may have a Br value of around 9,000 G, Ferrite magnets have a Br value around 3000 G.
It’s essential to remember that these values can vary depending on the manufacturer and the specific grade of the magnet.
2. Considering the temperature of the usage environment
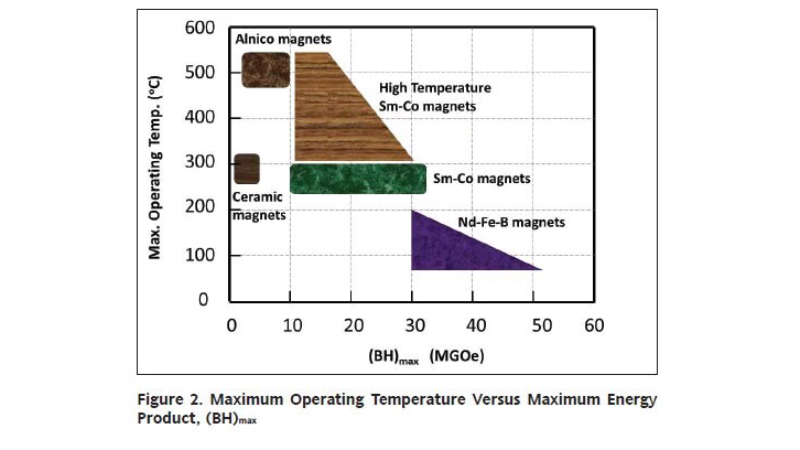
Operating temperature range:
When choosing a permanent magnet for a particular application, it is crucial to consider the temperature of the usage environment. The material properties of permanent magnets, such as coercivity and remanence, are sensitive to and change with temperature, so it is vital to choose a magnet material that can withstand the operating temperature range of the application without experiencing significant changes in its magnetic properties.
Maximum temperature:
It is important to know the maximum temperature the magnet will have to withstand, as high reverse fields can demagnetize a magnet. We should either avoid operating the magnet at temperatures that could cause demagnetization or design the circuit to prevent the magnet from being subjected to critical demagnetizing fields at those temperatures.
If you’re interested in Temperature Effects On Permanent Magnets, click it to explore more!
Table (3) of Critical Temperatures for Various Materials
Magnet Types | Grade | Curie Temperature/°C | Maximum Working Temperature/°C |
Sintered NdFeB | N | 310°C | 80°C |
Sintered NdFeB | M | 340°C | 100°C |
Sintered NdFeB | H | 340°C | 120°C |
Sintered NdFeB | SH | 340°C | 150°C |
Sintered NdFeB | UH | 350°C | 180°C |
Sintered NdFeB | EH | 350°C | 200°C |
Bonded NdFeB | 310-340°C | 100-150°C | |
SmCo5 | 700-750°C | 250°C | |
Sm2Co17 | 800-850°C | 300-350°C | |
AlnNiCo | 750-850°C | 450-550°C | |
Ferrite | >450°C | 250°C |
Temperature can significantly impact the maximum energy product (BHmax) of a permanent magnet. As shown in Table (2), the maximum operating temperature of a magnet can affect its BHmax. Generally, samarium-cobalt (SmCo), alnico, and ceramic magnets can be used at elevated temperatures, while neodymium-iron-boron (NdFeB) magnets can only be used at relatively lower temperatures.
If the maximum operating temperature is below 150°C, NdFeB magnets may be a good choice for high-performance systems due to their high BHmax. However, if the maximum operating temperature is above 180°C, SmCo magnets may be a better choice due to their high BHmax and temperature tolerance.
It is important to consider the temperature range of the application when selecting a magnet material to ensure optimal performance.
3. Considering Corrosion Resistance
Corrosion can be a concern when choosing a permanent magnet because it can lead to a loss of magnetism in the magnet, which can affect its performance in an application. It can also cause the magnet to weaken or break over time, reducing its lifespan.
Neodymium magnets are highly susceptible to corrosion due to their high iron content (64-68%), making them vulnerable to rust and other forms of corrosion in damp environments.
Suppose a magnet, particularly a NdFeB magnet, will be used in a potentially corrosive environment. In that case, it may be necessary to apply a coating to the magnet to protect it against rust and other forms of corrosion. Click Coatings for Neodymium Magnets to explore more!
Samarium cobalt magnets are much more resistant to corrosion, even when left uncoated. They are also part of the rare earth family of magnets and offer good magnetic performance, although they are not as strong as neodymium magnets.
Alnico and Ferrite magnets are both known for their corrosion resistance, although they do not offer the same level of magnetic performance as neodymium and samarium cobalt magnets.
4. Considering the Cost
The cost of permanent magnets can vary significantly depending on the type of magnet and the size and quantity of the magnets you purchase. The cost of permanent magnets can range from a few cents to several hundred dollars per magnet.
SmCo magnets are generally the most expensive type of permanent magnet, followed by NdFeB magnets, Alnico magnets are less expensive than NdFeB magnets, and Ferrite magnets are the least expensive type of permanent magnet.
Neodymium: Medium Cost
Although neodymium is also a rare earth element, Neodymium Iron Boron (NdFeB) magnets are generally less expensive than Samarium Cobalt (SmCo) magnets. Due to the high strength of NdFeB magnets, they are widely used in many different applications,
Samarium Cobalt: High Cost
Samarium Cobalt magnets are known for their high heat stability and powerful strength-to-weight ratio. Still, they come at a high cost because of the high price of rare earth elements Samarium and cobalt.
They are a strong and durable option but may not be the most cost-effective for some applications.
Alnico: Low Cost
Alnico magnets are made primarily of aluminum, nickel, and cobalt, relatively inexpensive materials. They are not as strong as NdFeB or SmCo magnets but have high-temperature stability and lower cost.
Ceramic: Low Cost
Ferrite magnets, also known as ceramic magnets, are the least expensive type of permanent magnet, but they are also the weakest.
5. Choosing A Reliable Supplier
When selecting a supplier for your permanent magnets, it is important to prioritize reliability. You want to work with a trustworthy supplier who puts quality first. Look for a supplier with a proven track record and industry experience, and make sure they stand behind their work.
At JdaMagnet, we are a family-owned company with over 23 years of experience in the magnet industry. We pride ourselves on being a reliable supplier and are sure to get the best value for your investment. Contact us for more information!
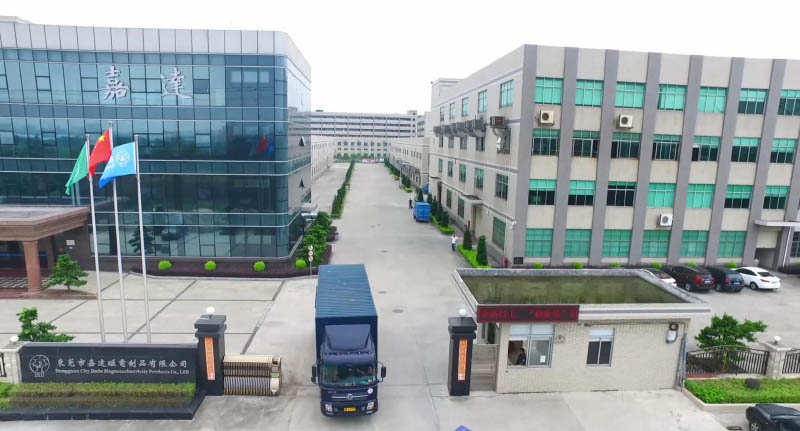
Conclusion
Choosing the right magnet for the specific application is crucial for cost-effectiveness and performance. A magnet that is too strong for the application will result in unnecessary costs, while a magnet that is not strong enough may not provide sufficient performance.
Therefore, we should consider several factors when choosing a permanent for our design, such as required magnetic strength, usage temperature, corrosion, cost, and a reliable supplier. By considering all these factors, we can make an informed decision and choose the right magnet that will meet our needs and provide the desired level of performance without overspending.