As a manufacturer of magnetic materials, I often encounter questions about the differences and similarities between samarium cobalt (SmCo) magnets and neodymium iron boron (NdFeB) magnets. Both types of magnets are important rare earth magnets with similarities and differences.
One key difference between SmCo and NdFeB magnets is their performance at high temperatures and in corrosive environments. SmCo magnets are more resistant to demagnetization and corrosion than NdFeB magnets. On the other hand, NdFeB magnets have a much stronger magnetic field and are generally less expensive to produce than SmCo magnets.
Despite these differences, both types of magnets have some essential similarities. They are rare earth magnets with very high maximum energy product (BH Max) and high coercivity (resistance to demagnetization). They are also both widely used in a variety of commercial applications.
There are many other factors to consider when deciding which type of magnet is best for a particular application. It is important to carefully evaluate the specific needs of your application and consider the trade-offs between the various characteristics of these two types of magnets.

Let us explore a more detailed comparison of samarium cobalt (SmCo) magnets and neodymium iron boron (NdFeB) magnets:
Manufacturing Similarities:
Both samarium cobalt (SmCo) magnets and neodymium iron boron (NdFeB) magnets are made using sintering processes, which involve several steps. Here is a summary of the main steps involved in the production of rare earth magnets:
- Mining: The raw materials for rare earth magnets, including neodymium, samarium, cobalt, and other elements, are mined from ore deposits worldwide.
- Production of powder: The raw materials are ground into fine powder and mixed in the appropriate ratio to achieve the desired magnetic properties.
- Milling: The magnetic powder is milled, or finely ground, to improve its uniformity and consistency.
- Pressing: The milled magnetic powder is pressed into the desired shape, typically using a hydraulic press or an isostatic press.
- Annealing: The pressed magnets are subjected to a heat treatment process called annealing to improve their magnetic properties and increase their stability.
- Cutting: The magnets are cut into the desired shape and size using specialized cutting equipment.
- Grinding: The magnets may be ground to achieve a smooth, precise finish and to meet specific tolerances.
- Surface finishing: The magnets may be subjected to a surface treatment process to improve their corrosion resistance and increase their stability.
Making rare earth magnets involves combining physical and chemical processes to produce high-quality magnets with specific magnetic properties. The specific steps and processes may vary depending on the type of magnet produced and the desired characteristics.
If you’re interested in the detailed steps involved in producing NdFeB magnets, please click Here.
Crystal Structure Similarities:
SmCo and NdFeB magnets have anisotropic crystal structures, meaning their magnetic properties are highly directional and concentrated in a specific direction.
SmCo magnets have a hexagonal crystal structure, which gives them highly directional magnetic properties in the north-south direction. The hexagonal arrangement of atoms in SmCo magnets allows for the tightly concentrated magnetic field that contributes to their strong magnetic properties.
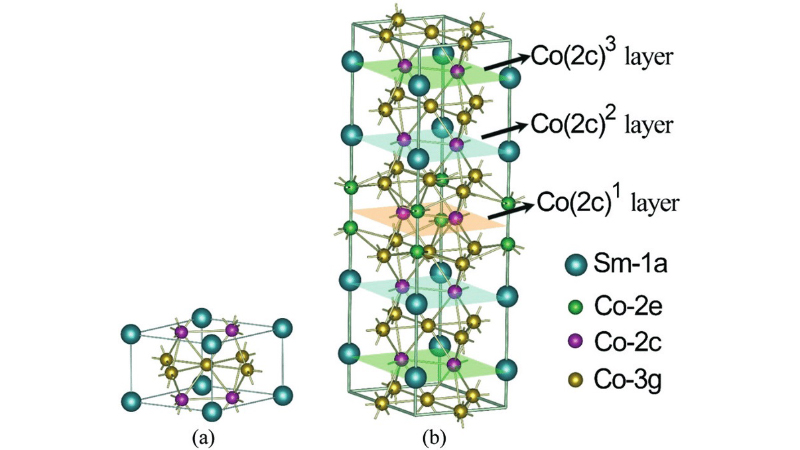
Image Credit: Researchgate
NdFeB magnets also have an anisotropic crystal structure, specifically a tetragonal crystal structure. This arrangement of atoms gives NdFeB magnets highly directional magnetic properties in the north-south direction. The tetragonal crystal structure of NdFeB magnets allows for the tightly concentrated magnetic field that contributes to their strong magnetic properties.
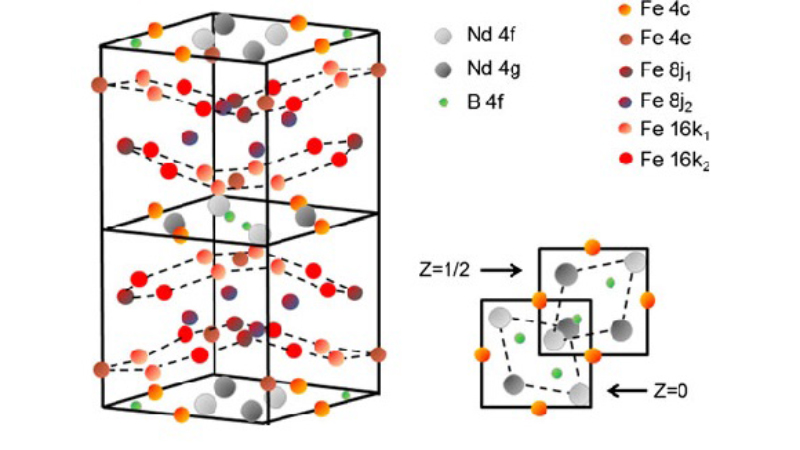
Image Credit: Researchgate
Composition Difference:
Samarium cobalt (SmCo) magnets are made from a combination of samarium, cobalt, and other rare earth elements. The specific composition of SmCo magnets may vary, but they generally contain around 20-30% samarium, and the remainder is cobalt.
Neodymium iron boron (NdFeB) magnets are made from a combination of neodymium, iron, and boron. The specific composition of NdFeB magnets may also vary, but they generally contain around 30-45% neodymium, around 50-60% iron, and the remainder is boron.
The specific composition of SmCo and NdFeB magnets can affect their magnetic properties, including their magnetic strength and temperature stability. For example, the high cobalt concentration in SmCo magnets contributes to their higher temperature stability. In contrast, the high neodymium concentration in NdFeB magnets contributes to their strong magnetic field.
Corrosion Resistance Difference:
Samarium cobalt (SmCo) magnets and neodymium iron boron (NdFeB) magnets have different levels of corrosion resistance due to their different compositions and the conditions under which they are used.
SmCo magnets have a higher corrosion resistance than NdFeB magnets due to their composition. SmCo magnets contain cobalt, which is a highly corrosion-resistant element. In addition, the high-temperature stability of SmCo magnets makes them less susceptible to corrosion due to the formation of surface oxides, which can protect the magnet from further corrosion. As a result, SmCo magnets are often used in corrosive environments where NdFeB magnets may not be suitable.
NdFeB magnets, on the other hand, have a lower corrosion resistance than SmCo magnets due to their composition. NdFeB magnets contain iron, which is prone to corrosion in specific environments. In addition, the high magnetic field strength of NdFeB magnets can cause them to generate heat when they are used, which can further contribute to corrosion. As a result, NdFeB magnets may require surface treatments or protective coatings to improve their corrosion resistance in specific applications, including coatings that can pass a 1000-hour salt fog test, which is a very intensive corrosion test.
Both magnets can be used in various applications where corrosion resistance is a key factor. Still, it is essential to carefully evaluate the application's specific needs and choose the appropriate coating or surface treatment to ensure the desired level of corrosion resistance.
Brittleness Comparison:
Samarium cobalt (SmCo) magnets and neodymium iron boron (NdFeB) magnets are brittle materials. This means they are prone to cracking or breaking when subjected to mechanical stress or shock.
However, SmCo magnets are generally more brittle than NdFeB magnets. This means that they are more prone to cracking or breaking under mechanical stress or shock and may be more challenging to handle and more prone to damage during manufacturing or assembly.
SmCo magnets need not be coated for corrosion protection in many cases, as they can withstand exposure to many corrosive environments without significant degradation. However, there may be situations where it is desirable to coat SmCo magnets for other reasons, such as to improve their cleanliness or to increase their resistance to chipping.
Temperature Coefficients Difference:
The temperature coefficient of a material refers to the change in its physical properties with temperature. For magnets, the temperature coefficient is often expressed as a percentage change in magnetic flux density per degree Celsius (B/°C).
Samarium cobalt (SmCo) magnets and neodymium iron boron (NdFeB) magnets have different temperature coefficients due to their different compositions and magnetic properties.
SmCo magnets have a low-temperature coefficient, meaning their magnetic properties are relatively stable over a wide temperature range. SmCo magnets can maintain their magnetic properties up to around 300°C, making them suitable for high-temperature applications where other magnets may lose their magnetic properties.
On the other hand, NdFeB magnets have a higher temperature coefficient than SmCo magnets. This means that their magnetic properties are more sensitive to changes in temperature, and they may lose their magnetic properties at lower temperatures than SmCo magnets. NdFeB magnets can typically maintain their magnetic properties up to around 80-100°C, depending on the specific composition and conditions of the magnet.
Hence, the temperature coefficient of SmCo and NdFeB magnets is important when selecting a magnet for a specific application. SmCo magnets are generally more suitable for high-temperature applications due to their low-temperature coefficient. In contrast, NdFeB magnets may be more suitable for lower-temperature applications where their higher temperature coefficient is not a concern.

Magnetic Field Strength Difference:
Magnet strength is essential when selecting a magnet for a specific application, as it determines the strength of the magnetic force that the magnet can exert.
Samarium cobalt (SmCo) magnets and neodymium iron boron (NdFeB) magnets have different magnet strengths due to their different compositions and magnetic properties. The appropriate magnet strength will depend on the specific needs of the application.
SmCo magnets have a moderate magnet strength compared to other types of magnets. They are typically able to produce a magnetic field of around 8-12 kG (kilogauss) at the surface of the magnet. SmCo magnets are known for their high-temperature stability and resistance to demagnetization, making them suitable for applications where these properties are essential.
On the other hand, NdFeB magnets have a much stronger magnet strength than SmCo magnets. They are typically able to produce a magnetic field of around 12-14 kG (kilogauss) at the surface of the magnet, and they have the highest BH Max (Maximum Energy Product) of any permanent magnet available today. This makes NdFeB magnets very suitable for use in applications where a strong magnetic field is required, such as motors and generators.
Coercivity Comparison:
Both samarium cobalt (SmCo) magnets and neodymium iron boron (NdFeB) magnets have high coercivity compared to other magnet materials.
SmCo magnets have an exceptionally high coercivity, which makes them very stable under different conditions and resistant to demagnetization. This makes SmCo magnets suitable for use in applications where the magnet needs to maintain its magnetic properties over a long period, even in opposing magnetic fields or high temperatures.
NdFeB magnets also have a high coercivity, although it is generally lower than that of SmCo magnets. This means that NdFeB magnets may be more susceptible to demagnetization under certain conditions. However, they can still be suitable for use in certain applications where their lower coercivity is not a concern.
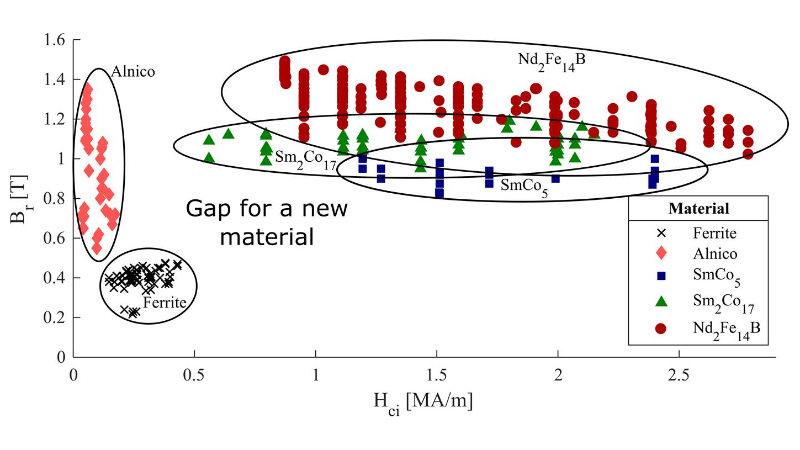
Application Difference:
Samarium cobalt (SmCo) magnets and neodymium iron boron (NdFeB) magnets are both important types of rare earth magnets used in various applications. The appropriate choice for a specific application will depend on the specific needs and requirements.
Here is a more detailed breakdown of the common applications of SmCo and NdFeB magnets:
Samarium cobalt (SmCo) magnets application:

- Aerospace: SmCo magnets are often used in aerospace applications due to their high-temperature stability and resistance to demagnetization. They are used in various aerospace components, including actuators, generators, and motors.
- Defense: SmCo magnets are used in various defense-related applications due to their high-temperature stability and resistance to demagnetization. They are used in components such as guidance, radar, and weapons systems.
- Medical devices: SmCo magnets are often used due to their high-temperature stability and corrosion resistance. They are used in MRI machines, pacemakers, and medical pumps.
- High-temperature motors and generators: SmCo magnets are used in high-temperature motors and generators due to their ability to maintain magnetic properties at high temperatures. They are used in applications such as electric vehicle drivetrains and aircraft generators.
- Heavy industrial and marine applications: SmCo magnets are often used in heavy industrial and marine applications due to their high-temperature stability and corrosion resistance. They are used in components such as motors and generators for heavy machinery and marine vessels.
- Downhole applications in the oil and gas industry: SmCo magnets are used in the oil and gas industry due to their high-temperature stability and corrosion resistance. They are used in components such as drilling tools and sensors.
Neodymium iron boron (NdFeB) magnets application:
- Motors and generators: NdFeB magnets are commonly used in motors and generators due to their strong magnet strength and high energy product (BH Max). They are particularly suitable for small, high-power motors and generators, automotive electric vehicle (EV) drive, and accessory motors.
- Sensors: NdFeB magnets are often used in sensors due to their strong magnet strength and ability to generate a highly directional magnetic field. They are commonly used in magnetic field sensors, position sensors, and proximity sensors.
- Electro-acoustics: NdFeB magnets are commonly used in electro-acoustic applications such as loudspeakers, headphones, and microphones due to their strong magnet strength and ability to generate a highly directional magnetic field.
- Consumer products: NdFeB magnets are also used in various consumer products, including mobile phones, computer hard drives, and other electronic devices.
Conclusion:
SmCo and NdFeB magnets are vital to many high-tech applications and play important roles in various industries.
As a manufacturer, we must carefully consider the specific characteristics and properties of SmCo and NdFeB magnets when selecting a magnet for a specific application. We will keep up to date with the latest developments and improvements in magnet technology, helping to ensure that we are using the most appropriate magnet for your needs.
If you have any specific questions about your application or need more information about using SmCo or NdFeB magnets, please don’t hesitate to consult our expert. We can provide valuable guidance and assistance in helping you to choose the best magnet for your needs.